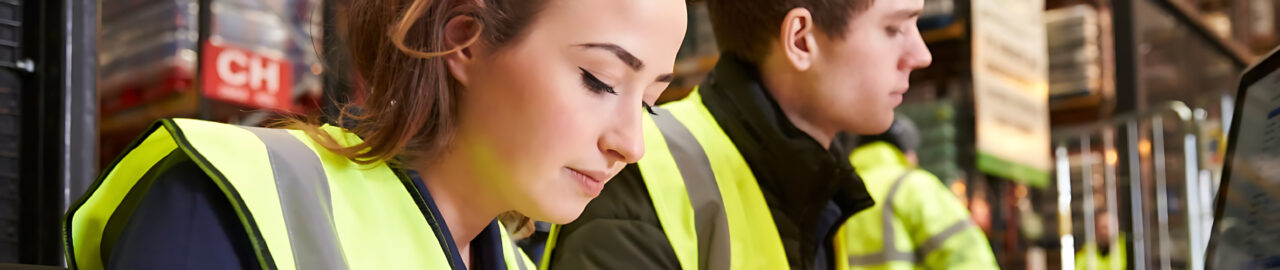
How your profile seals and moulded parts are produced
From drawing to tools, to series of profiles – M+R provides a one stop shop for tailor-made, individual and economical solutions.
Our experts can provide personal advice and support in producing a drawing to be turned into a tool by our technicians. Are your requirements particularly challenging? In our involvement in numerous projects, we have proven that we can master even the most complex geometries.
Of course, before a series is produced, we create a few samples for approval. Then we produce the rubber profiles and seals your require in any quantity desired. Due to the dimensions of our extrusion machinery, production can only start economically from a weight of approximately 300kg. We can also create moulded parts in limited numbers.
What can you expect from us?
- Our highly qualified staff are an excellent resource for the construction sector. Years of experience in manufacturing tools means that we are extremely flexible and customer focused. In practice, this means that the time between initial contact and delivery of the products you require, can be as low as 6 to 8 weeks.
- This depth of experience is just as essential in producing the optimal solution for your rubber profile. Using specially selected materials means that we can provide a wide spectrum of profile qualities.
- Our extrusion is done on high performance extrusion systems with salt bath vulcanisation. The advantages of this process are:
- large format profiles and large production runs
- low production costs due to high throughput speed
- optional processes for high quality peroxide crosslinking mixes
- controlled and careful removal of profiles without belt removal pressure points
- We use modern, fully automatic injection moulding presses for corner vulcanisation. We can therefore vulcanise very complex corner configurations.
- By vulcanising individual cross sections it is possible to make almost any profile cross section into a closed frame. Special hot corner moulds considerably increase quality and durability.
- Additionally, we manufacture customised, vulcanised rings, fixed lengths and profile sections using high performance cutting and stamping systems.
- We are continually expanding our production of moulded rubber parts using injection moulding because of the increasing demand for this process. The advantage over extrusion of this type of manufacture is that completely customised solutions can be produced.
Our manufacturing techniques
Tool production
Thanks to our highly developed tool construction facilities, at M+R – Profiles we can manufacture even difficult profile geometries economically and with precision.
Extrusion
We use three salt bath lines with diameters from 90mm to 120mm, and our production facilities are also equipped with a coextrusion line.
Injection Molding
We manufacture sealing frames with precise joins by using modern injection moulding presses.